
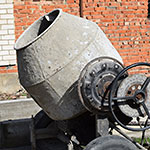
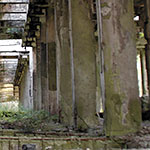

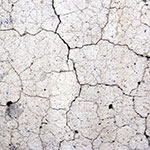

How Natural Pozzolans Improve Concrete
Natural pozzolans are magmatic in origin and widely available worldwide, although like most naturally-occurring compounds, all pozzolans are not created equal. The performance-enhancing properties vary from material to material, and then from deposit to deposit in the same material class. (Note: The pozzolan from an individual deposit, however, is likely to be very consistent, load to load.) Nor is the mineralogical makeup the only qualifying factor; the physical characteristics of the pozzolan also affect performance. You can be assured that the natural pozzolans marketed by our NPA member-producers have been thoroughly tested and the performance results clearly quantified. That test data is available from our natural pozzolan producers. Testing samples are also available by contacting a member-producer.
Natural Pozzolan Types
Natural pozzolans fall into two main category types: raw and calcined. The difference is in the origin of calination:
RAW POZZOLANS: In the fiery heart of a volcano, water mixes with liquidfied molten stone, pressure builds...to eruption. Magma is blasted violently into the atmosphere, water flashes to steam, magma foams and explodes into sun-darkening clouds of fast-cooling bits of stone or tephra, eventually drifting back to earth—as fully calcined pozzolanic material. These lightweight, amorphous, frothy little stones and ash are drifted, gathered and packed together by millennia of wind and water into massive deposits of tuffs, pumices, pumicites and other rhyolitic materials.
CALCINED POZZOLANS: Calcined pozzolans—derived from clays and shales—which are themselves derived of magmatic materials, reach that usefully reactive pozzolanic state in the fiery roar of a carefully calibrated furnace. The rock softens, trapped moisture flashes, and the material is transformed into a pozzolanic amorphous state. Like mined raw pozzolans, calcined pozzolans are then, if necessary, milled and graded to the ideal size to ignite a pozzolanic reaction within curing concrete.
Natural pozzolan products are further differentiated by particle size and chemical composition and offered in a variety of particle sizes in order to work effectively in various concrete mix designs and specifications.
Pozzolan Defined
Pozzolan is defined in ACI 116R as: “…a siliceous or siliceous and aluminous material, which in itself possesses little or no cementitious value but will, in finely divided form and in the presence of moisture, chemically react with calcium hydroxide at ordinary temperatures to form compounds possessing cementitious properties.” Pozzolans, then, are not simply SCMs and mitigators against chemical attack, but also transformers: repurposing deleterious calcium hydroxide into a cementitious compound that magnifies performance. To further burnish the pozzolan position, natural pozzolans can even do their magic while replacing a percentage of the necessary Portland cement in the mix design; anywhere from 5% to 40% replacement of OPC, which serves to significantly reduce the carbon footprint of every concrete pour.
See also: Frequently Asked Questions
The Performance Boost
The key to an effective pozzolan is the bold completeness of the reaction it ignites within hydrated concrete. The pozzolanic reaction is a secondary, super-charger reaction to the primary reaction of Portland cement and water.
Simply put, pozzolans improve concrete by converting problem-causing Calcium Hydroxide (CH)—a by-product of the hydraulic reaction between water and cement powder—to additional Calcium Silicate Hydrate (CSH)—the glue that binds the concrete aggregate.
The true wonder of the pozzolanic reaction is that it both consumes the source of the problem and repurposes it to desirable CSH. The pozzolanic reaction process continues—even after the cement-water hydration process wanes—until either the CH or the pozzolan is consumed.
The benefits of the pozzolanic reaction are many:
Reduce Heat of Hydration Damage and Escalate Strength: Natural pozzolans reduce the heat of hydration anywhere from 10 - 40% during the first 100 hours, depending on the ultimate mix design, thus lowering the threat of thermal cracking and allowing for a cooler, controlled set. After 100 hours the cement-water hydration process wanes while the pozzolan mixes continue to hydrate until one of the two remaining hydration agents, Calcium Hydroxide or natural pozzolan, have been consumed. This slow pozzolanic hydration process can continue for months and even years, bringing the long-term strength of the natural pozzolan-based concrete well beyond that of ordinary Portland cement concrete.
Inoculate Against Chemical Attacks: When the CH migrates out of the concrete’s interior via capillary action, it leaves behind a maze of porosity that both weakens the concrete and allows for the future ingress of water. This infiltrating water can contain sulfates, chlorides, and other damaging chemicals. In cold climates, the invasive water will freeze, causing freeze-thaw damage to the concrete. Not all of the CH migrates out of the concrete, and what remains will combine or react with other chemicals that may be present within the concrete matrix, or introduced later through the aforementioned means of ingress. Natural pozzolans are so effective at consuming the problem-causing CH that natural pozzolan boosted concretes are typically high sulfate resistant.
Fortify Resistivity: Chloride penetration resistance is a key factor in protecting reinforcing steel embedded in the concrete from corrosion and ultimately protecting the concrete from failure caused by expansion of the iron oxide hydrate (rust). Natural pozzolan contributes to a concrete matrix so densely packed that liquids and/or gases cannot penetrate to cause the steel to corrode.
Mitigate ASR: As concrete hardens, natural pozzolans readily react with calcium hydroxide as it becomes available, trapping any present alkali inside the densified cement paste, which alleviates capillary action and virtually eliminates alkali-silica reactions and efflorescence. Research clearly indicates natural pozzolan-blended cements are highly resistant to the ravages of Alkali Silica Reaction.
Stop Efflorescence: Natural pozzolans will mitigate or eliminate unsightly efflorescence in concrete. Efflorescence is the white powdery substance that forms on the surface of some concretes that do not have a pozzolan in the mix design.
Additional Benefits
Healthy and Safe: Natural pozzolans are free of crystalline silica and other hazardous materials. While waste-product artificial pozzolans are saddled with occasional variability in their chemical and physical properties, a carefully mined and refined natural pozzolan is the environmentally safe, consistent choice.
Reduces the Carbon Footprint: The production of cement requires 'burning' of limestone at high temperatures. This process consumes a large amount of carbon based fuel, and, as the limestone is heated, it releases additional carbon dioxide into the atmosphere to form lime, the key component in cement. The production of Portland cement accounts for approximately 5% of all carbon emissions annually worldwide. Natural pozzolan can replace up to 40 percent (by weight) the Portland cement in a concrete mix as a Supplementary Cementitious Material (SCM) helping to offset the cement’s carbon footprint while enhancing its performance and durability.
Workability and Set Times: Raw natural pozzolan-based mix designs have set times which are not significantly longer than the 100% cement. Some calcined natural pozzolans, such as Metakaolin, can actually shorten set times and increase both high early and long term strengths.
The Natural Pozzolan Association (NPA) is a network of natural pozzolan producers working to improve the performance and durability of the nation’s concrete infrastructure.
NATURAL POZZOLAN ASSOCIATION
100 East 155 South, Malad City, ID 83252
208.252.2808 • info@pozzolan.org